THE FIRST “TEST LAB” DEDICATED TO ADDITIVE SCIENCE
At ASTRO, we don’t just pull test bars. We aim to accelerate the potential of your hardware with faster results, reduced costs, and unwavering reliability—fueling innovation without limits. After all, you shouldn’t be the last to launch.
QUALIFICATION IS THE CATALYST THAT SHOULD IGNITE CONFIDENCE, NOT EXTINGUISH INNOVATION.
Our Goal: Keep our customers ahead in a rapidly evolving industry
ASTRO partners with aerospace and space tech companies to integrate validation protocols into materials and processes. Our collaborations drive industrialization of advanced manufacturing technologies by aligning systems development with production theories and mechanics.
We specialize in the AM validation, qualification and certification of aerospace materials, launch vehicle components, satellite technologies, and autonomous vehicles.
through focused qualification and Certification pathways, astro drives the industrial-scale adoption of advanced manufacturing. by exploring mathematical complexities in manufacturing optimization and managing the production horizontal, we algorithmically redefine capabilities and tackle the challenges of vALIDATING COMPLEX FLIGHT COMPONENTS.
mATERIAL DEVELOPMENT portfolio
LPBF | SLS | SLM | DMLS | EBM
ALUMINUM
•
AlSi10Mg
CP1
Scalmalloy
Al4047, Al-6061, Al-7075
F357
A6061-RAM2
NICKEL/COBALT
•
Inco625, Inco718
Hastelloy
ABD900
L605, Haynes25, Haynes 282
M-M509
Monel
STEEL
•
SS 316
SS 15-5
SS 17-4
SS 310
SS 420
TITANIUM
•
Ti6Al4V
Ti6Al2Sn4Zr2Mo
Titanium Aluminide
COPPER
•
GRCop42
CuCrZr
C18150
CuSn10
CuNi
IRON
•
Invar
FeNi
REFRACTORY
•
Niobium C103
Tantalum
Tungsten
STANDARD TESTING SERVICES
-
Tensile (Elevated & Cryogenic)
High Cycle Fatigue (Load)
Low Cycle Fatigue (Strain)
Impact Testing
Bend Testing
Compression
Universal Hardness
-
Microstructural Analysis
Density/Porosity
Grain Size Determination
Surface Roughness
Surface Contamination
Phase Formation
-
Tap and apparent density of a powder sample
Microstructure, texture, and grain size of powder and printed specimens (SEM)
Chemical composition of the powder and printed coupons (EDS)
PSD, morphology, flowability, aspect ratio, etc. of a powder sample
-
CNC Machining
Wire EDM
Polishing / Finishing
Passivation
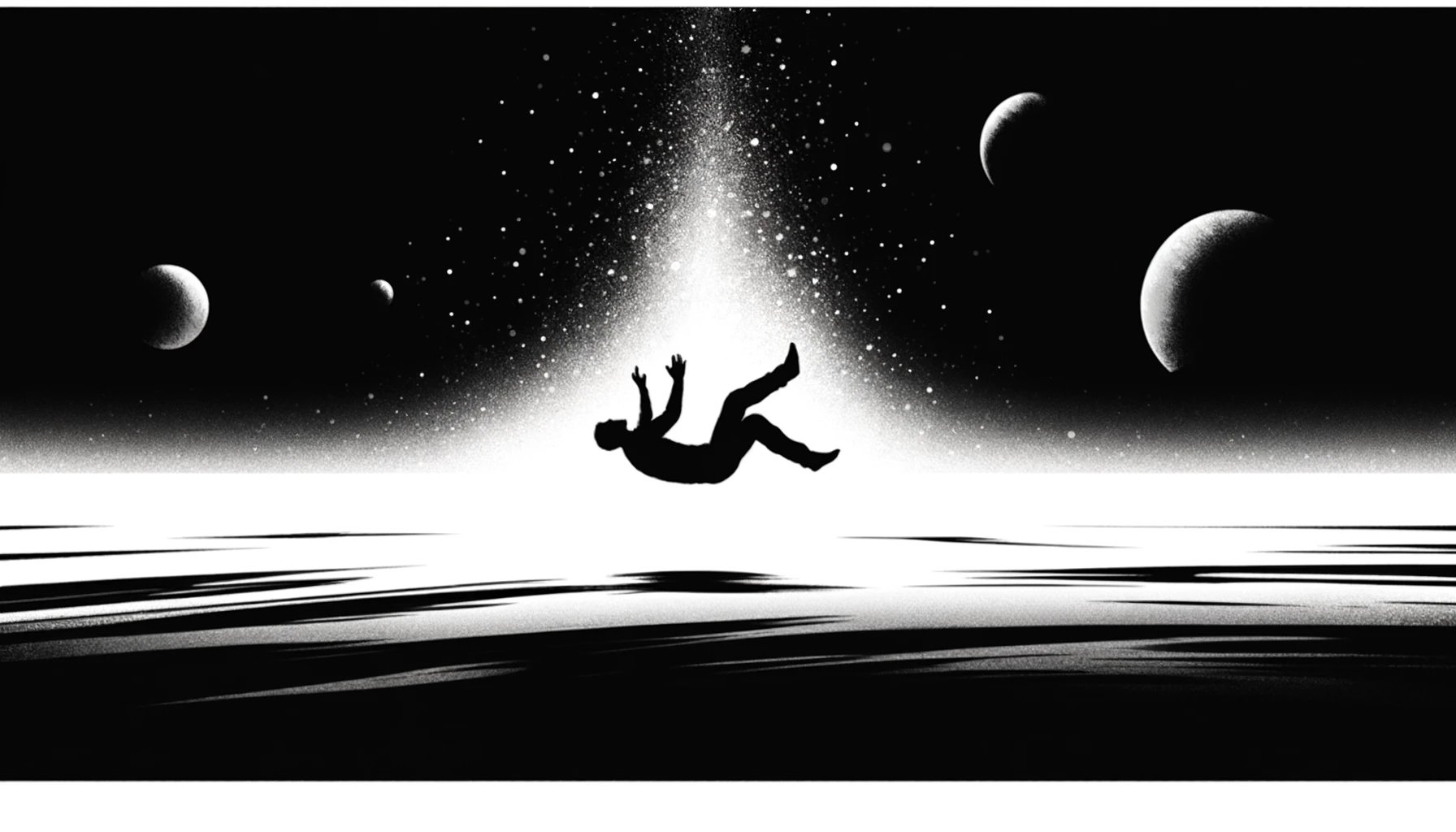